Offshore Fixed Platform
Wind Turbines
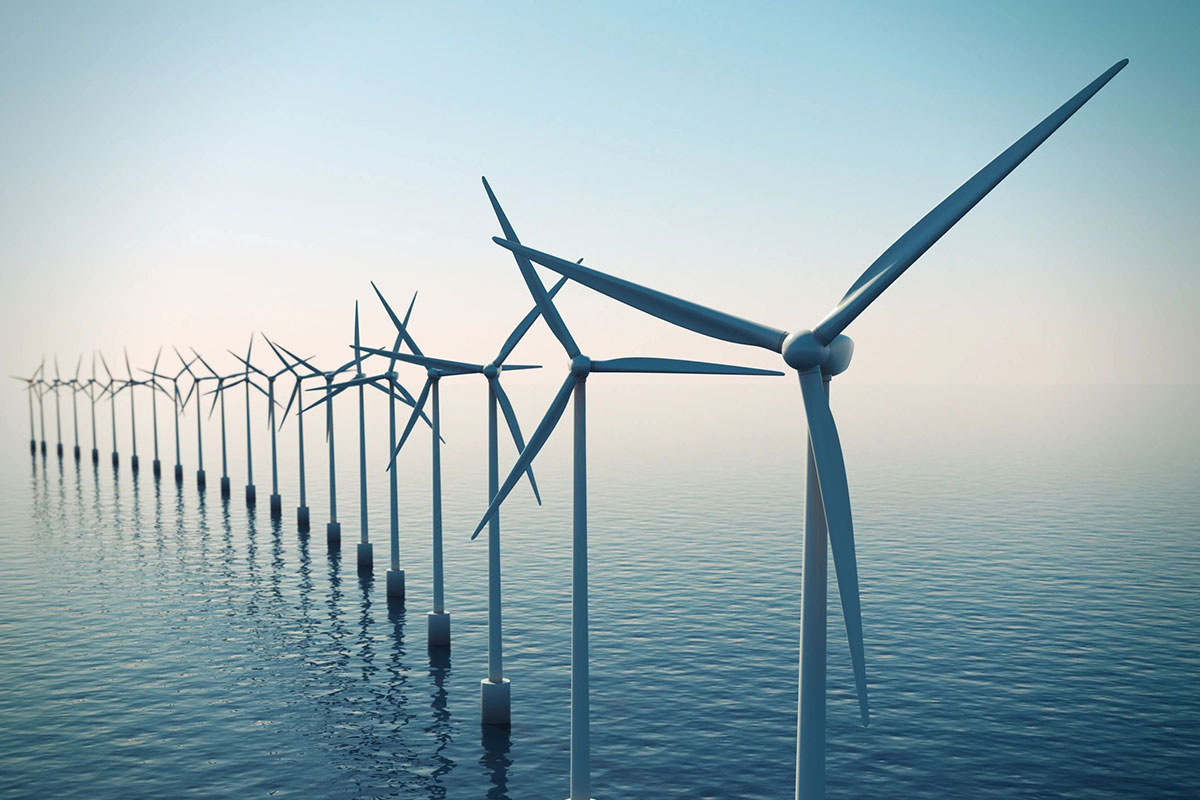
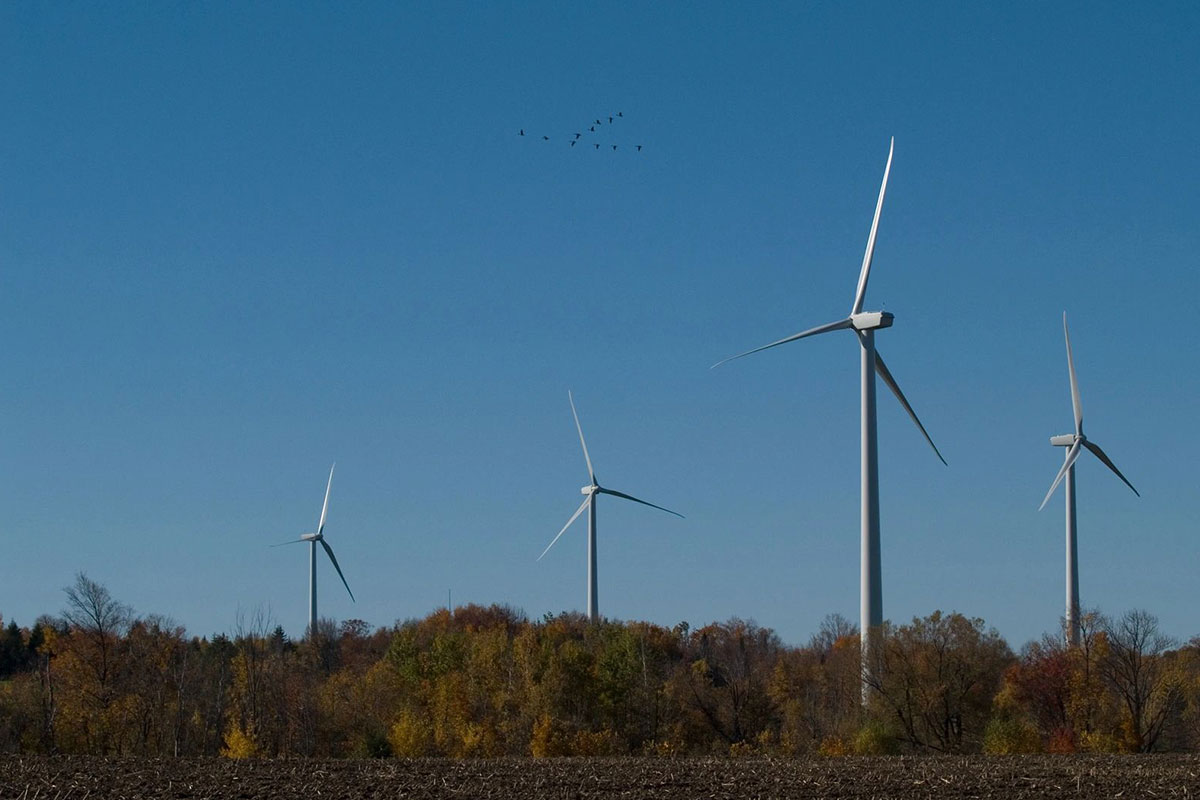
Onshore
Wind Farms
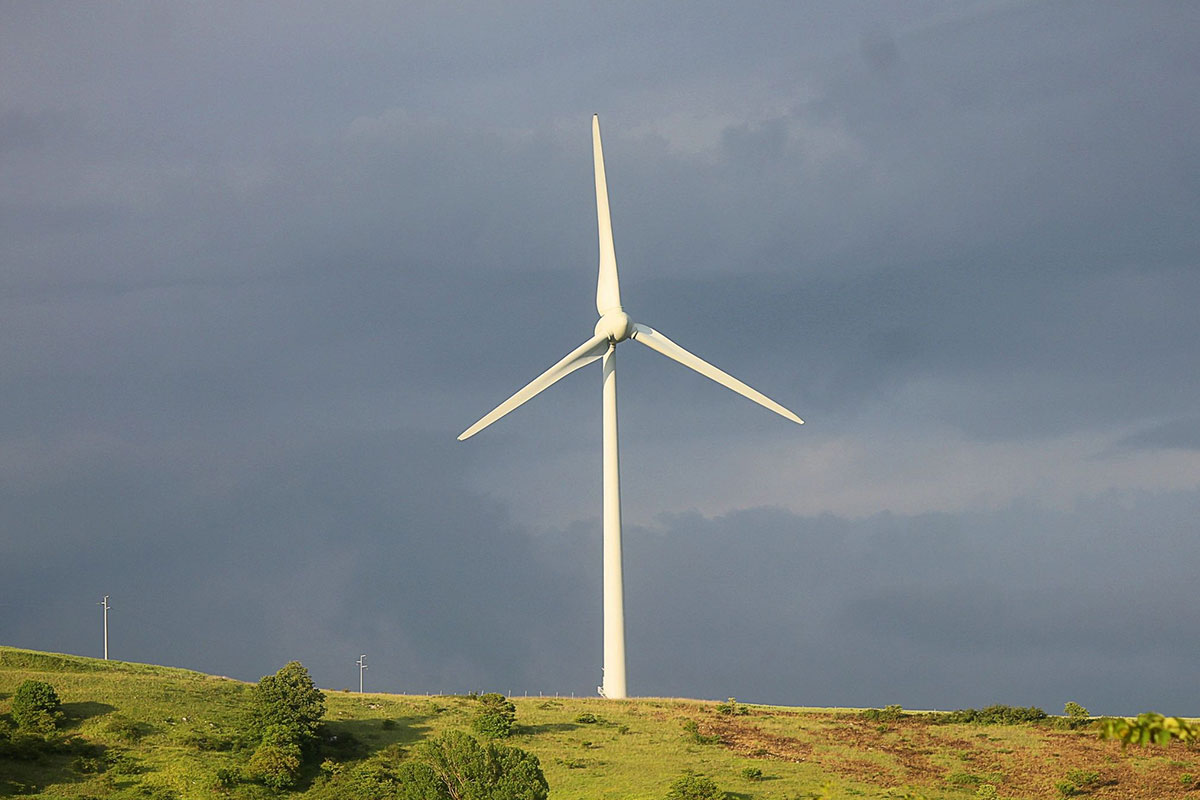
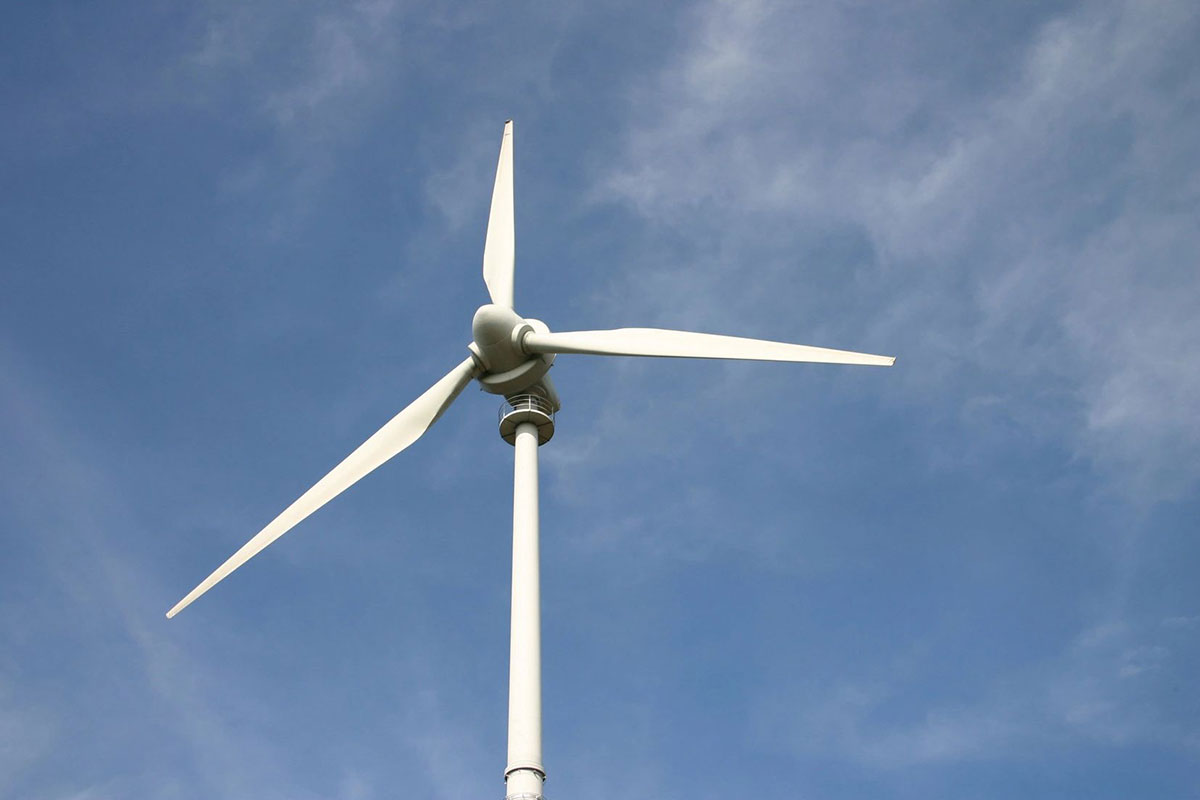
Onshore Distributed
Wind Turbines
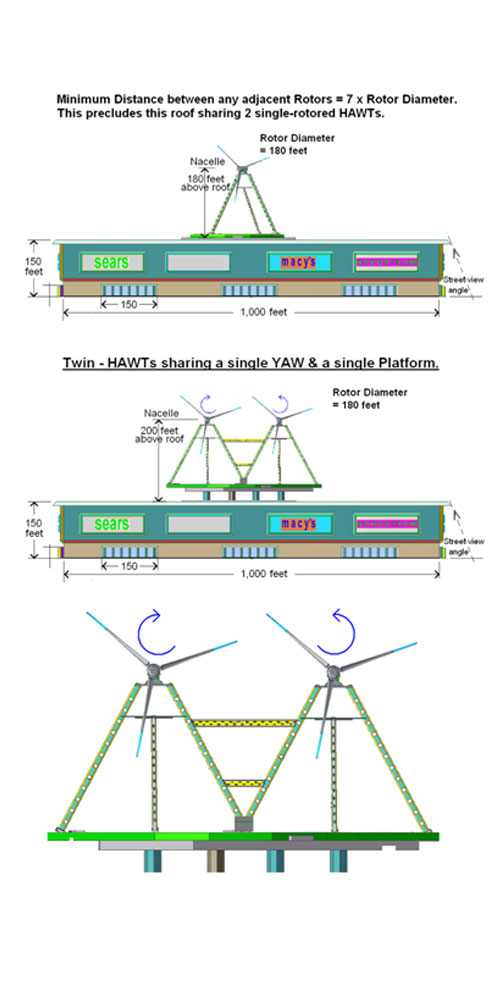
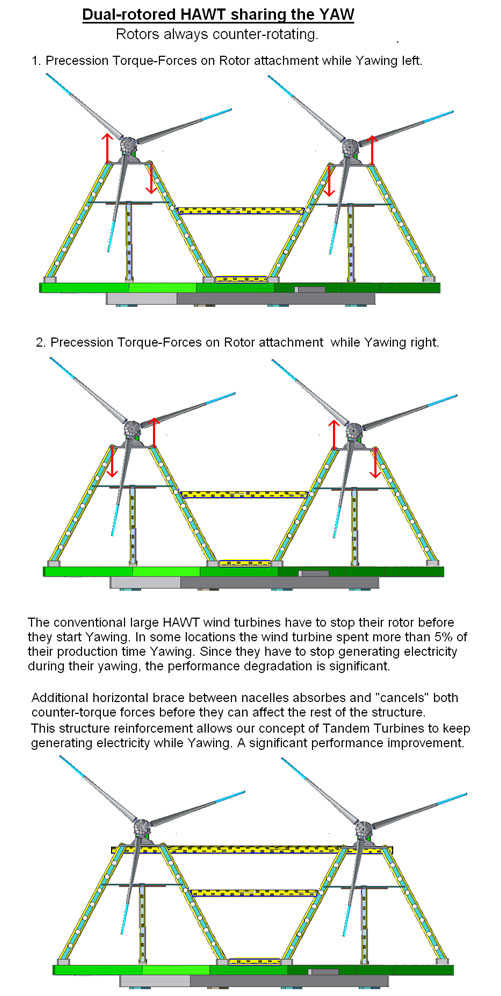
Offshore Floating Platform
Wind Turbines
“Sway-tolerant” Single or Dual-rotored HAWT Wind Turbine with Tripod-like stability.
Novel Wind Turbine concept for Off-shore Floating or Fixed Platforms.
ABSTRACT: Novel Wind Turbine patent-pending concept is introduced.
This concept with novel platform-level YAW Ring is well suited for both Floating or Fixed Platforms. Weight and top-heaviness reduction is significant. Further top-heaviness decrease is derived from the YAW mechanism moved from the top of the tower to the platform level.
The tripod support structure removes the bending moment singularity of the conventional Wind Turbine tower platform base attachment. The weight of the turbine, as well as the bending moments can now be distributed via a tripod over a wide circular yaw ring using a lighter “lattice” tripod construction.
Further significant stabilityimprovements are the floating platform sway motion de-coupling from the wind turbine. It is accomplished by a Self-adjusting capability to negate the angle sways of its floating platform. This is performed by a telescoping tiltrod. This tiltrod also functions as a third leg of a tri-pod support.
The re-positioning the turbine’s Yaw at the enables the Tandem Wind Turbine concept, since the common platform base Yaw can be nor shared by two HAWT wind turbines. The Dual-Rotored HAWT with common Yaw base essentially doubles the energy density of any Off-shore Array.
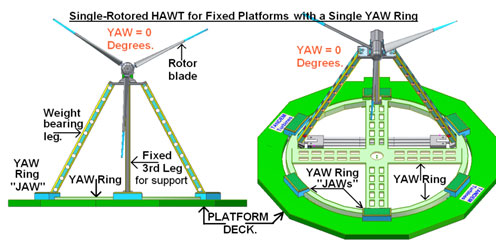
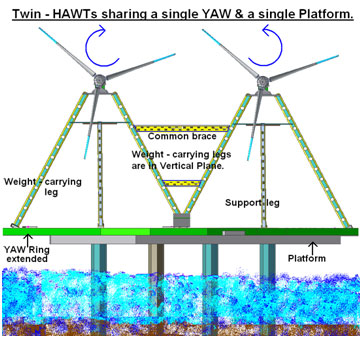
Principle of operation
Float picture below is fictional shown only as a reference. Our wind turbine can be used with many different types of floating platforms. The point is that because it is clearly more stable, as well as Sway-tolerant, the float below could be less massive and use less steel
The tripod tower design also removes the problem of the HAWT tower leaning away from its normally 90 degree angle to “horizontal” resulting in 2 major problems inherent to the conventional HAWTs described below on page-2.
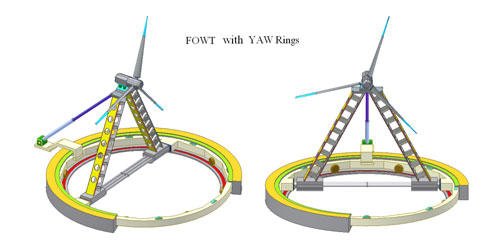
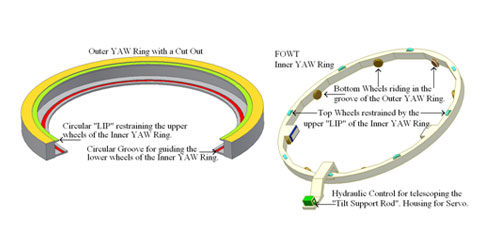
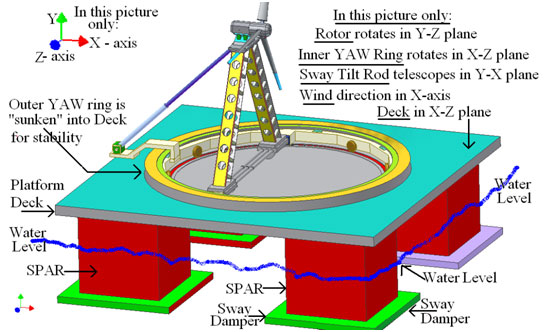
Sway problems inherent to the conventional
HAWTs afloat.
Sway Tilt-Rod principle of operation:
a) The sway of the tower (due to waves and/or wind forces on rotor) which is non-existent in the non-Float off-shore or on-shore wind turbines is a major structural problem for the FOWTs at the tower root attachment to the platform, as well as at the Tower split at the YAW mechanism, just below the nacelle.
The picture below adjusts the Turbine tower such that its rotor’s rotation plane always stays parallel to gravity and perpendicular to the incoming wind stream.
b) The sway of the tower also deflects the plane of rotor rotation from being parallel to gravity and perpendicular to the incoming wind stream.
Now the rotor plane deflection messes up the carefully optimized Angle of Attack of the rotor’s blades. The blades lose some or all lift force generation capability, which creates the torque force and the rotation. This leads to greatly diminished capability to convert the wind kinetic energy into the mechanical torque force.
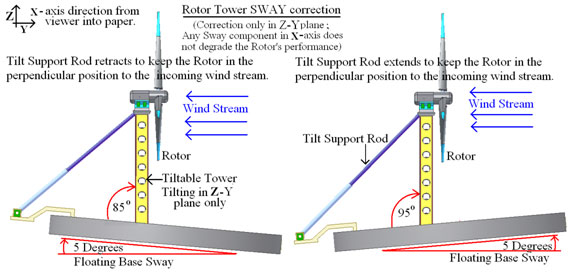
Installation advantage
Is shown in the picture below when the tower is lowered during the towing into the final location. At the arrival at the final location, the telescoping “Sway tiltrod” is used to erect the tover to the fully upright position.
Sheding the destructive energy during the wind storms.
The Sway tiltrod is used to lower the rotor into much safer position to better shed the wind forces. Towing back to a safe harbor to avoid hurricanes is also easier and faster.
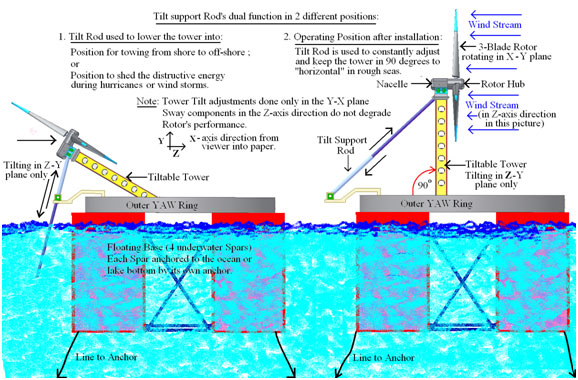
We have patented 2 different embodiments of the platform motion de-coupling by a tiltrod.
- Decoupling the Turbine rotor with its pivoted support tripod.
This is shown above and in greater detail on the next page.
- Decoupling the Turbine Rotor and its nacelle only.
The sway motion decoupling is likely faster and more responsive since the tripod support is not moved. Therefore, no base pivots required.
This is shown on the next page.
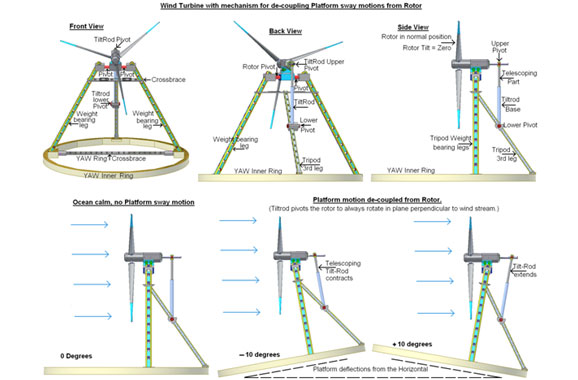
ARRAY configurations
Rotor blades of the conventional wind turbines rotate crosswise perpendicular to the wind flow, creating massive turbulent wake. Therefore the minimum distance between 2 adjacent wind turbines is typically 8 to 10 times the rotor diameter.
The advantage of 2 Turbines sharing a single platform.
The swept rotor area vs the total weight greatly improves when 2 wind turbines share a single platform. Our novel patent-pending concept enables this. See picture below.
Going from one to two turbine platform sharing:
For example, by adding an additional turbine the combined rotor swept area doubles (increases by 100%) yet the total weight increase by only about 20% if the single turbine weight is only 20% of the floating platform.
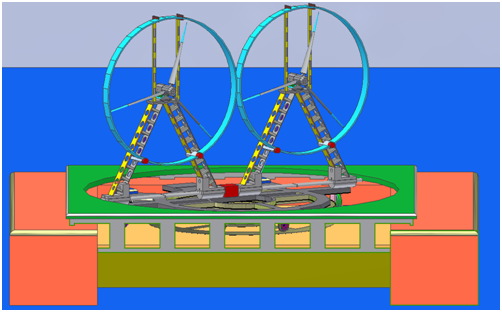
Impact in the emerging Off-shore Floating wind markets and industry.
Our patent-pending concept has the potential to overcome the primary weakness of conventional HAWTs (Horizontal Axis Wind Turbines) unstable & top-heavy requiring massive & expensive underwater floating platforms. Furthermore, conventional HAWTs cannot share the same platform due to their turbulent Rotor “downwash”. This allows the multiple BoosterHAWT wind turbines to share a single floating platform, resulting in higher “energy density” and lower overall cost.
Proposed Initial work in Model Built and Testing Stage
Energy conversion efficiency modeling vs cost. Building several complete scaled models with both passive and active Yaw mechanisms. Investigating passive YAW latency trade-offs. Proof of concept. Measuring the Sway tolerance latency. Creating and optimizing algorithms for the Servo motors/actuators. Evaluating the weight savings of transferring the YAW from the top of the tower to the automatic passive YAW at platform level. Experimenting with gyroscopic recession force absorption by the telescoping tiltrod.